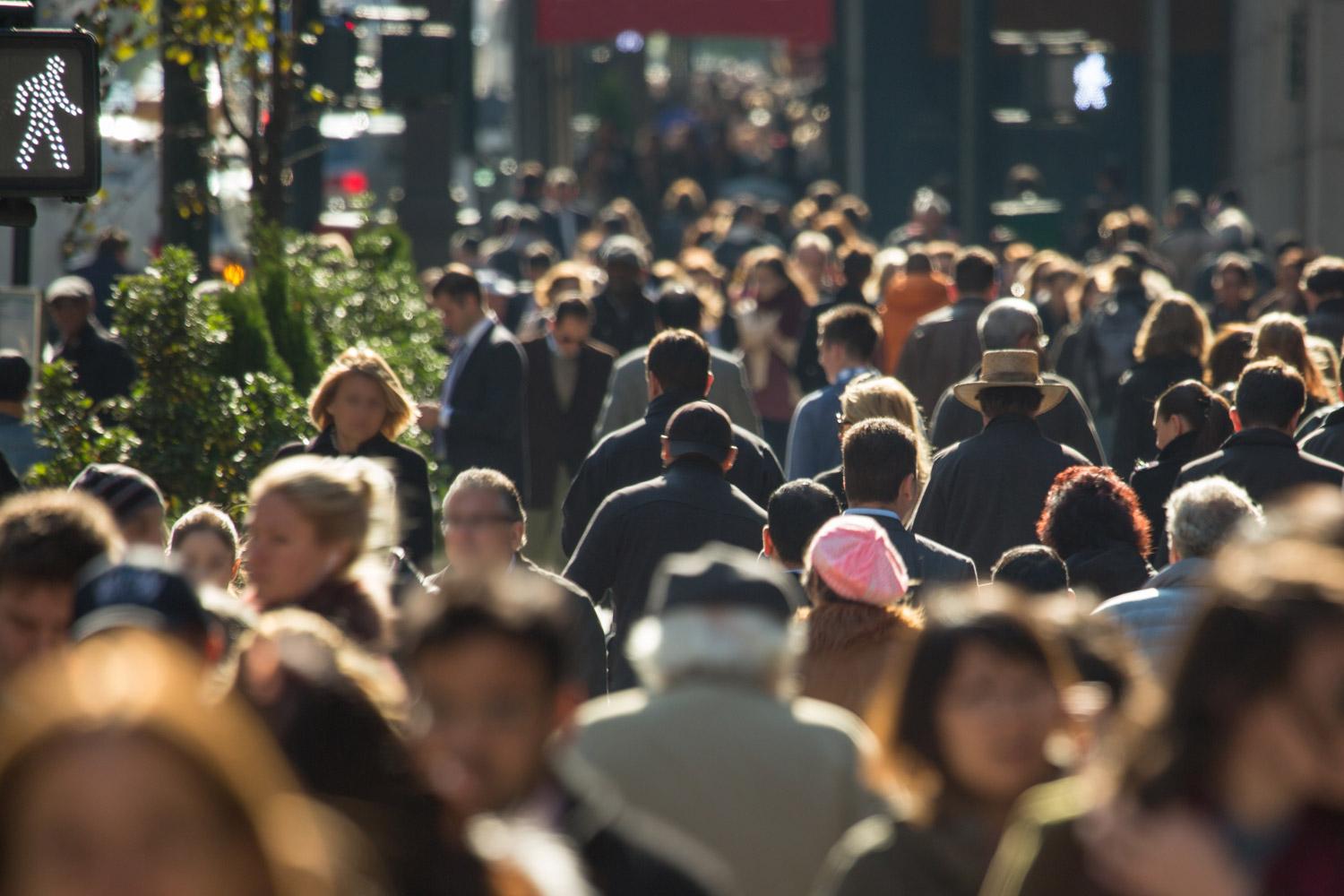
My Smore newsletter
The Advancements in Artificial Intelligence for Predictive Maintenance
Artificial Intelligence (AI) has been transforming various industries, and the manufacturing industry is no exception. Predictive maintenance, one of the most crucial aspects of the manufacturing industry, has been revolutionized by the implementation of AI. Predictive maintenance is a technique that helps to predict when a piece of equipment or machinery is likely to fail and prevent unplanned downtime. With the integration of AI, predictive maintenance has become more efficient and cost-effective, enabling manufacturers to enhance their operational performance and reduce maintenance costs.
In traditional predictive maintenance, maintenance tasks are performed based on a predetermined schedule, such as after a certain number of operating hours or at regular intervals. This approach, however, has several drawbacks, including over-maintenance, where maintenance is performed too frequently, and under-maintenance, where maintenance is performed too infrequently. Over-maintenance leads to increased maintenance costs, while under-maintenance leads to equipment failure and unplanned downtime.
The integration of AI in predictive maintenance enables manufacturers to overcome these challenges and make more informed maintenance decisions. AI algorithms analyze data from various sources, such as sensors and equipment logs, to predict when a piece of equipment is likely to fail. This information is then used to schedule maintenance tasks in a more proactive and predictive manner.
One of the key benefits of AI in predictive maintenance is the ability to identify patterns and anomalies in equipment behavior. AI algorithms can detect patterns in equipment performance that are not visible to the human eye. This information can then be used to predict when a piece of equipment is likely to fail, allowing maintenance teams to perform the necessary tasks before a failure occurs.
Another benefit of AI in predictive maintenance is the ability to optimize maintenance schedules. AI algorithms can analyze data from various sources to determine the most effective maintenance schedule for each piece of equipment. This information can then be used to schedule maintenance tasks at the most optimal time, reducing the frequency of maintenance tasks and reducing maintenance costs.
In addition to the benefits outlined above, AI in predictive maintenance also enables manufacturers to reduce unplanned downtime. Unplanned downtime can have a significant impact on a manufacturing facility, resulting in lost productivity, increased maintenance costs, and decreased customer satisfaction. AI algorithms can help to predict when a piece of equipment is likely to fail, allowing maintenance teams to perform the necessary tasks before a failure occurs and reducing the likelihood of unplanned downtime.
In conclusion, the integration of AI in predictive maintenance has revolutionized the way maintenance is performed in the manufacturing industry. With the ability to predict when a piece of equipment is likely to fail, optimize maintenance schedules, and reduce unplanned downtime, manufacturers can enhance their operational performance and reduce maintenance costs. As AI continues to advance, it is expected that predictive maintenance will become even more efficient and cost-effective, providing manufacturers with new and innovative ways to improve their operations.
Learn more with Realclobber's informative news and blog section.