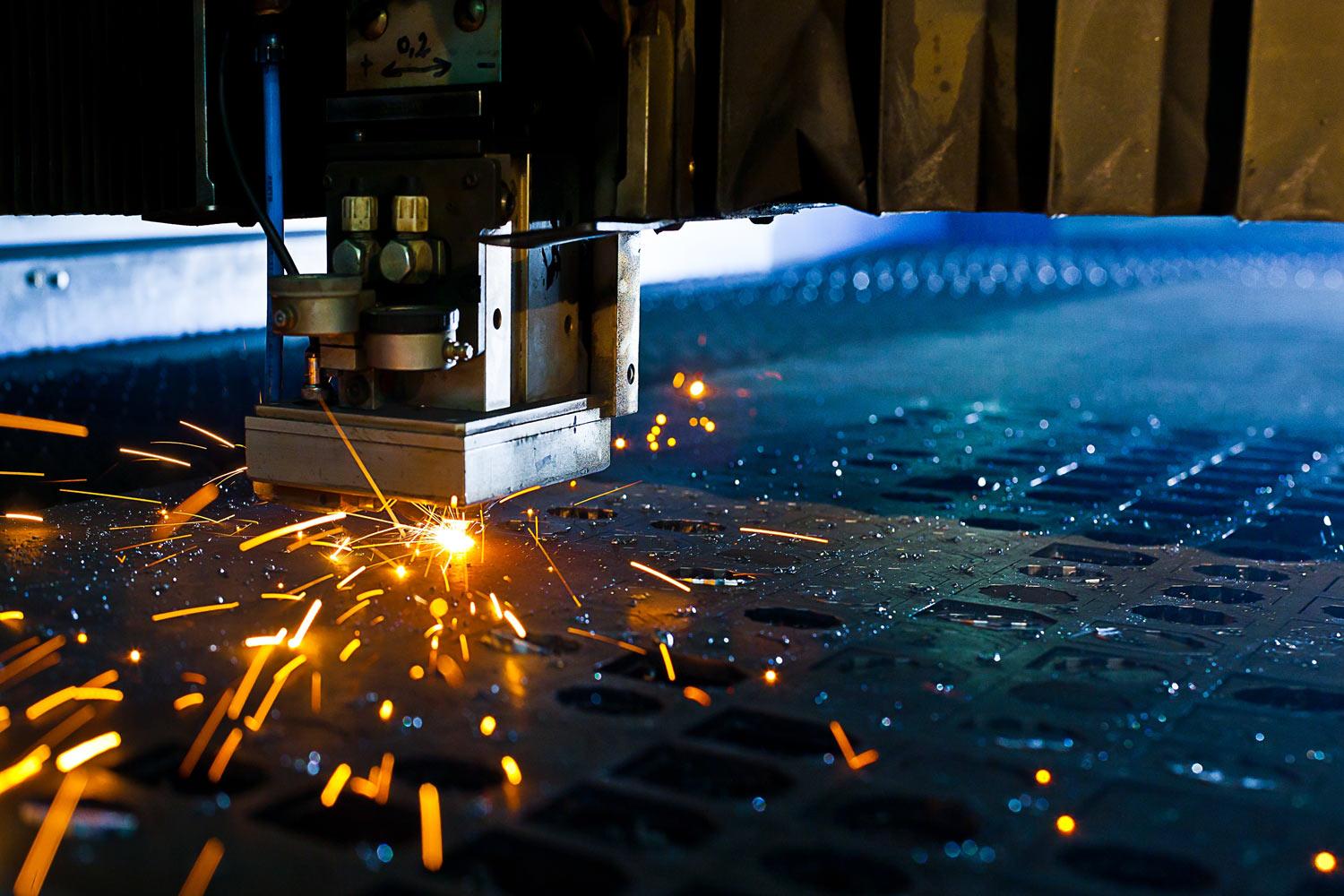
Secondary machining processes
Machining methods used in engineering
Machining processes
The manufacturing of engineered products or parts often requires the removal of material and some form of shape changing. This is known as 'secondary machining' or 'forming' Traditional secondary machining processes and the machines that perform them fall into three groups -turning, milling and drilling.
Turning
Turning is a process that uses a Lathe to produce a given shape, usually cylindrical. Lathes all have one thing in common: the workpiece is held in a chuck and rotated while being machined to shape by a single point cutting tool.
Lathes can be both manual and Computer Numerical Controlled (CNC).
Milling
This is a process used to shape products and parts by removing excess material to produce a range of simple and complex shapes. A Milling machine is different to a Lathe because the workpiece is clamped to the table or in a vice, the cutter rotates and removes the excess material. There are two main types of Milling machines - horizontal and vertical. In most cases, a universal milling machine combines both types of machine.
Drilling
In this process a drill bit is used to create circular holes in a workpiece. The drill bit usually has a straight shank that can be held in a drill chuck. To drill a satisfactory hole in any material, the correct drill bit must be selected. This can normally be found on a supplier's website. Good-quality drill bits can be expensive but the key to good drilling is keeping the cutting edge sharp.
1.3 Machine Tool Basics -- Lathe Cutting Tools -- SMITHY GRANITE 3-in-1
Crash Course in Milling: Chapter 1 - Basic Machine Anatomy, by Glacern Machine Tools
Basics: Drill Press
Safety while machining.
The most common causes for accidents while using a secondary processing machine are:
- Loose clothing snagging on a revolving part
- Flying pieces of material entering the eye.
- Hands or arms coming into contact with revolving surfaces/parts.
- Minor burns from hot material surfaces
You should always follow the correct procedures and wear the right Personal Protective Equipment (PPE) for the process that you are using. Goggles must be worn to protect the eyes, overalls/workshop coat must be worn to protect clothes and skin from hot metal chips and harmful liquids.