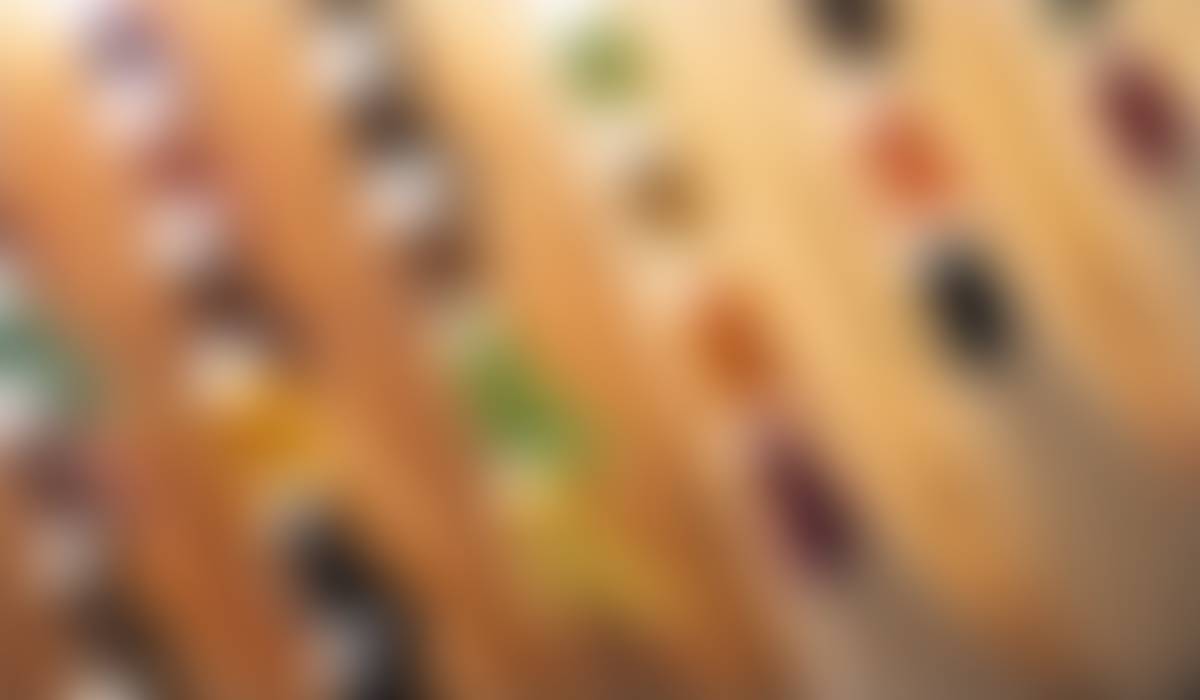
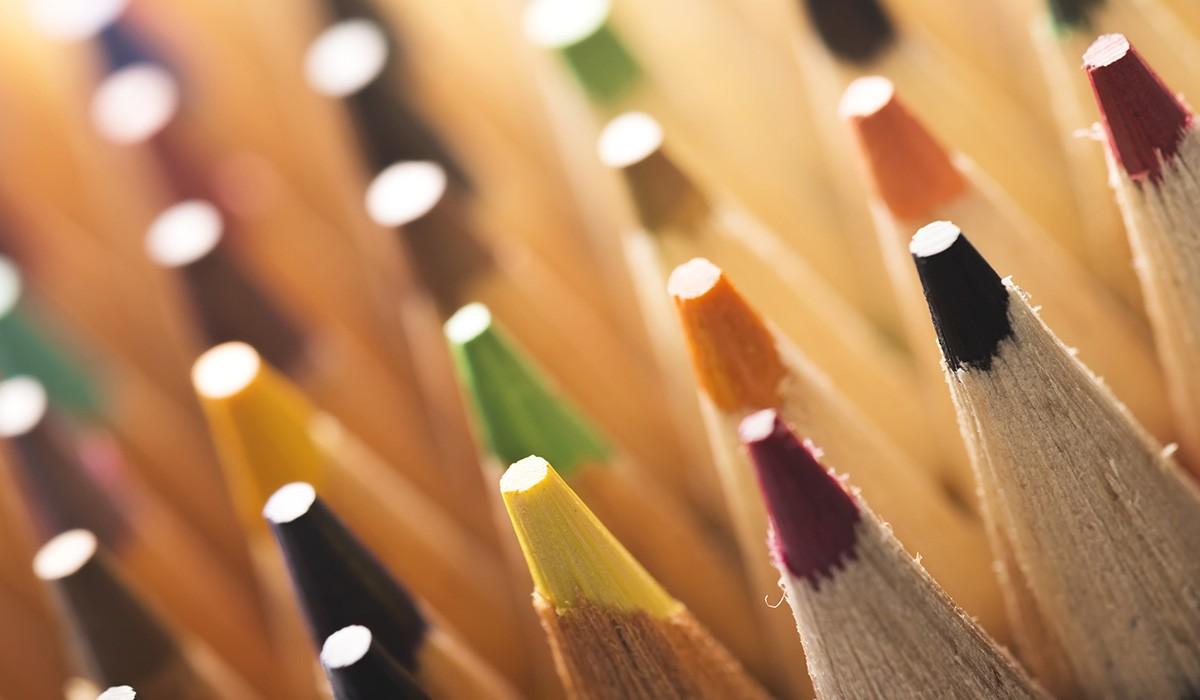
chjt
December 14th, 2024
What is Curable Reducer for Plastisol Ink
In the world of screen printing, plastisol ink is one of the most widely used ink types, particularly for its durability and versatility. However, achieving the perfect print requires more than just choosing the right ink. This is where the curable reducer for plastisol ink comes into play. At Plastisol Inks, we delve into the importance of this additive and how it enhances the screen printing process.
What is a Curable Reducer?
A curable reducer is a special additive used in chjt to adjust its viscosity, making it easier to work with during the screen printing process. It does not change the color of the ink but alters its consistency, allowing it to flow more smoothly through the screen mesh. This makes it particularly useful when printing on intricate or detailed designs.
Unlike other types of reducers, curable reducers are unique because they remain stable after the curing process. This means that once the printed material passes through the heat source, the reducer's effects are permanent, and the ink retains its intended properties, such as opacity, texture, and durability.
The Role of Curable Reducer in Screen Printing
Improved Printability: One of the primary functions of a curable reducer is to improve the workability of plastisol ink. It reduces the thickness or viscosity of the ink, ensuring that it flows more easily through finer mesh screens. This makes it easier to print fine details and complex designs without clogging the mesh.
Enhanced Color Accuracy: By reducing the viscosity, curable reducers can help ensure that the ink lays down more evenly. This is especially important when dealing with lighter or translucent colors, which may otherwise appear uneven or streaky. A well-mixed curable reducer allows for more vibrant and consistent color prints.
Better Registration: In multi-color printing, precise registration is essential for accurate and clean prints. Curable reducers help by making the ink easier to manage, allowing it to move through the screen with less resistance. This ensures that the print lines up perfectly without smearing or misalignment.
Faster Production Times: Curable reducers can help speed up production times by preventing clogging and ensuring smooth ink flow. This reduces downtime between prints and ensures a more efficient process overall.
Reduced Ink Build-up: Excessive ink build-up on screens can lead to print defects, such as ghosting or misprints. Using a curable reducer ensures that the ink maintains its proper consistency throughout the run, minimizing such issues.
In conclusion, curable reducers play an essential role in the screen printing process by enhancing the performance of plastisol inks. By improving printability, ensuring better color accuracy, and optimizing production efficiency, curable reducers help print shops deliver high-quality prints every time. For more information about curable reducers and how they can improve your screen printing process, visit our website at Plastisol Inks.