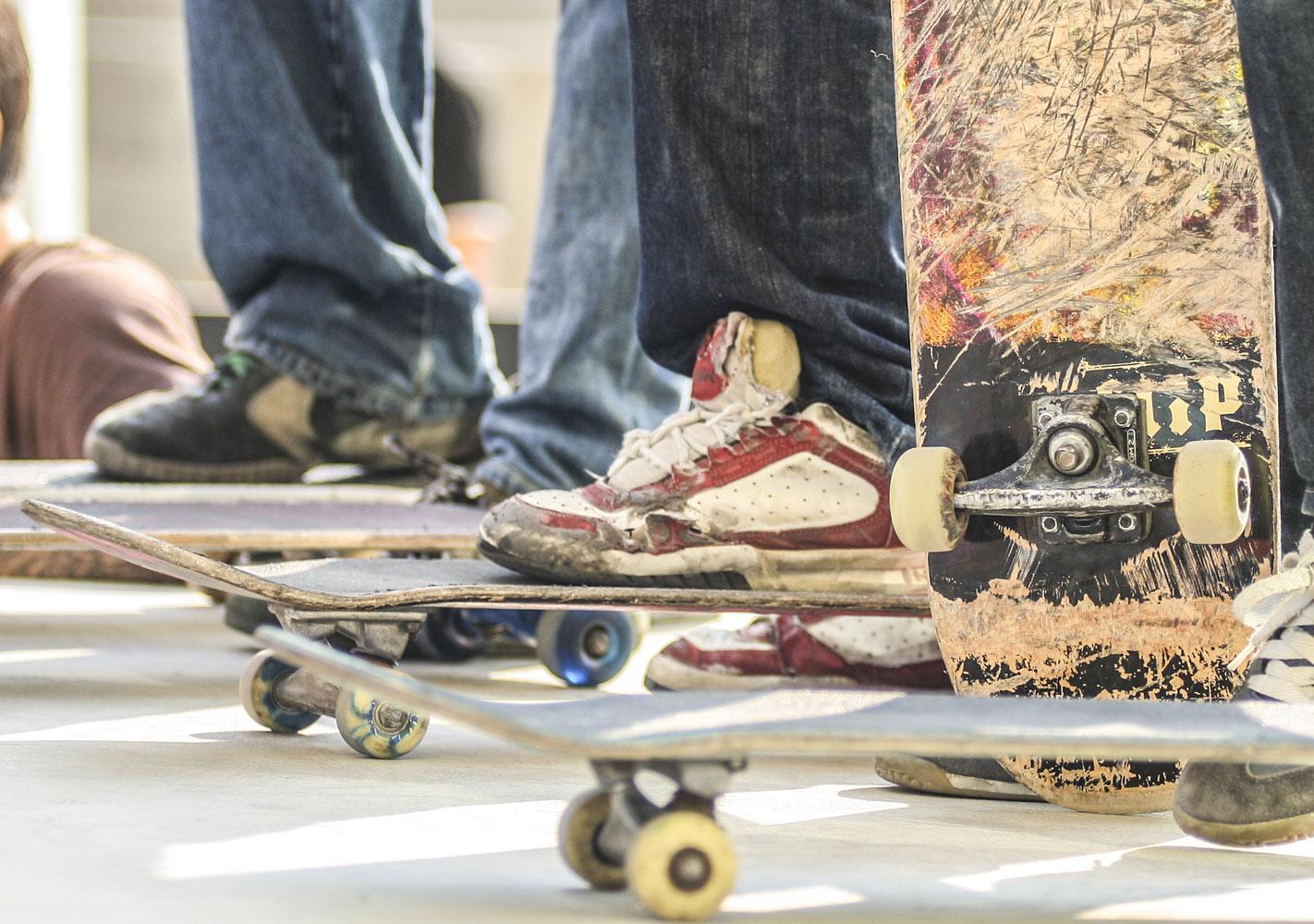
Mechanical engineering processes
Forming processes used in engineering
Forming
Complex shapes such as engine blocks, tools and equipment cannot always be achieved through traditional secondary machining processes. The two main forming processes that allow these parts to be made are casting and forging.
Casting
Casting is a process that usually involves pouring or injecting a liquid metal into a mould or tool. The mould contains a cavity that has been machined to the reverse/mirror image of the desired shape. The molten material is poured into the tool filling it up. It is then left to cool and solidify. The tool is then opened and the casting is then removed. Depending on the casting process used the product could be finished or require additional finishing on a secondary machining process, e.g. milling, turning or drilling.
How it's made - Metal casting
Sand casting
Used for large parts where dimensional accuracy is not as important as other features, e.g. manhole covers.
Semi-permanent and permanent mould casting
Used for products that requires use with water pressure and in larger quantities that sand casting as tooling costs are relatively high, e.g. pressure valves.
Investment casting
This is used for parts that have close dimensional tolerances and complex shapes such as compressor wheels for turbochargers.
Die casting
This process is used to manufacture large quantities of parts that require close tolerances and little machining after casting has taken place, e.g. Toy cars.
Forging
This is a process that involves a metal being heated up until it is malleable and then shaped by plastic deformation. It is usually achieved by applying a squeezing force (compression) such as a hammer blows using a large power press. Forging improves the physical properties of a metal by changing the direction of the grain flow to improve strength, toughness and ductility.
Drop forging
Produces a range of small to medium-size shapes with good dimensional accuracy and high production rates through hammering in a closed die, e.g. engine cams.
Press forging
This process uses a slow squeezing action to form the metal that penetrates the whole object making it suitable for forging large objects, e.g. landing gear.
Upset forging
Is used to create parts like the head of a bolt. It works by using bar stock material with on the end that needs to be shaped protruding from the tooling. A hammer blow is delivered that shapes the protruding end to the desired shape.
20 ton hydraulic closed die forging hammer forge bent axle for tank